摘要:介绍了以三菱可编程序控制器,模拟量输入模块,COM口232无协议通信模块和触摸屏面板为组合处理单元的配料称重控制系统的组成原理,给出了系统的主要程序设计流程。实践表明:该系统运行正确可靠且具有硬件结构简单和成本低廉的特点。控制模式:称重传感器、信号变送器+控制器+执行器+配方;控制器是上位机程序+PLC程序,执行器是指电磁阀和电动机电磁离合器等等。一、引言 配料秤重控制系统即将两种或两种以上的物料按一定重量配比自动定量加入到混合机内,经过混合达到预定要求后自动出料的过程。该系统广泛应用于化工,医药,饲料,建材,冶金等行业的配料混合过程控制。与传统继电器接触装置相比,PLC具有体积小抗干扰能力强和可靠性高等优点; 虽然PLC在数据处理和显示功能方面有些不足,但若采用性能稳定的计算机来完成数据采集与通信处理,不但便于提供处理精度和降低成本,而且便于通过计算机本身的COM通信接口进行数据输出和管理;选用三菱F900触摸屏代替常规显示器做人机界面,将使系统设计成本大为降低,使PLC与显示器的接口编程变得更加简单,并能使显示功能得到增强。 混凝土搅拌站控制计量系统中共有11个计量秤控制16中配料配重即11路传感器信号输入,11个变送器,每个计量秤都是3或4个传感器组成每组传感器并联或串联由4或6跟信号线接入传感器信号线接线盒,再接入TR200H变送器传感器信号是2MV/V,灵敏度高低信号传输,须经过变送器识别转换为模拟信号,送入PLC的模拟量信号采集模块; 整个控制系统无需秤重计量仪表与主控制台,只需传感器接线盒、信号变送器、接线柜、PLC、模拟量输入模块、通信模块、触摸屏,HZS(HLS) 系列混凝土搅拌站控制双机同步控制系统,主要硬件由两台计算机、高性能的微电脑控制器、人机界面、高速高精度的称重单元和国际著名低压电器组成,结合自主研发的专业控制软件实现混凝土生产的自动化控制,计量系统计量精度高,制造成本低; 在混凝土搅拌站电控系统的故障率调查中,计算机故障排在第一位,一旦发生故障将造成停机、停产。双机同步控制系统的两台计算机可同时也可单独完成对整个生产流程的控制和管理,当一台计算机出现故障时,可以由另一台计算机承担控制任务,从而在不需要人工干预的情况下,自动保证系统能持续进行生产控制,将因计算机故障的停机率降到最低; 传统上一般都采用工业计算进行生产过程的控制,但因工业计算机配件和软件的原因,一旦发生故障一般计算机维修人员都难以处理,给用户的维护带来了很大的困难和隐患,某某某电控通过技术进步,降低了对计算机的性能要求,不但可以使用工业计算机而且可使用标准计算机完成控制功能,方便了用户的维护和升级,可彻底解决用户的后顾之忧。1.高性能的硬件配置确保控制的稳定、可靠:(1)ADLINK 工业级计算机。(2)高性能长寿命的 MITSUBISHI PLC :超高速的运行速度,基本指令 0.08 μ s ,平均无故障连续运行 30 万小时。性能可靠。(3)MITSUBISHI 人机界面:全中文、宽视角、高速回应、性能可靠。(4)MITSUBISHI AD 模块: 500 μ s 高速转换, 1/20000 的分辨率。(5)主要低压电器采用 Schneider 、 ABB 、 Rmron 等世界知名品牌。
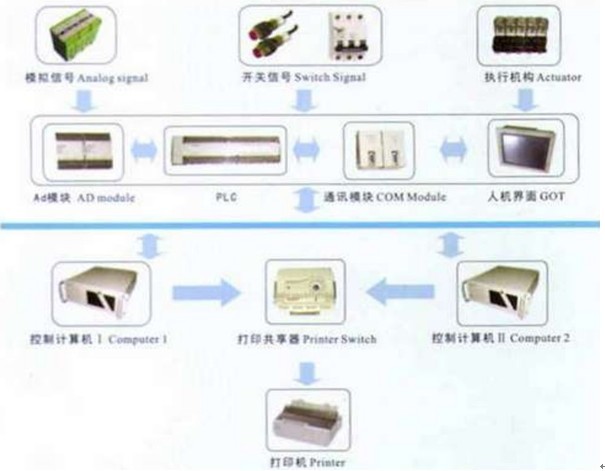
2.完善的控制功能:
(1)软件登陆和电子秤调校需要用户密码,有效的保证了重要生产数据的安全。
(2)全立体界面动画模拟生产工况,实时显示配料值、称量值、误差值等生产数据。
(3)可预先安排生产任务单并可重新调整生产顺序。
(4)自动根据批次产量和拌缸容量自动分配单罐产量。
(5)全中文快速校称并具有自诊断和提示功能,提供在线使用帮助。
(6)自动调整落差并具有趋势判断功能、负值自动修正、零位自动跟踪、按键去皮等。
(7)欠称自动补称、超称自动扣称,各种物料的计量和卸料允差范围皆单独可调。
(8)提供骨料含水率修正窗口,方便增砂减水。
(9)水计量可随时进行暂停和调整水配方。
(10)提供发货单加载功能,用户需要修改时可在办公软件完成发货单表格设计,加载到控制系统即可使用。
(11)数据管理系统方便用户对生产数据进行查询、浏览或将其输出到打印机。
3.操作简单、维护方便:
(1)自动、半自动、手动三种工作方式使生产流程的控制更为自如,真正体现出控制方便。
(2)傻瓜化参数设定,所有生产经验参数一键完成。
(3)生产流程、卸料顺序、搅拌时间计算方式可由用户根据生产需要和操作习惯进行自定义。
(4)拌缸卸料门在有效行程内可任意调整关闭、半开、全开的位置,由系统自动控制。并提供手动开门定位功能,操作简单、灵活、方便。
(5)全方位在线实时检测设备生产状态,并进行安全连锁管制。若出现异常工况,可准确提示设备故障点提醒工作人员进行定位查看与检修,实现故障定位排除。
二、系统组成及主要功能
2.1系统组成原理:
整个配料称重系统由搅拌仓﹑储料罐﹑称重传感器﹑料位计﹑三菱FX2N128点PLC﹑三菱特殊模块FX4AD模拟量输入采集模块与FX232IFCOM口通信模块﹑F900系列触摸屏和多个控制阀门等装置构成,分机械和控制两大部分。机械部分示意图如图1所示,
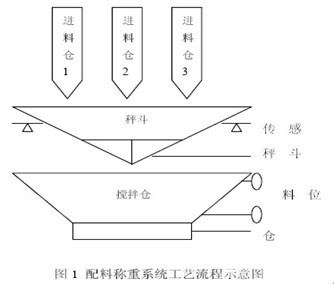
由进料仓﹑秤斗﹑搅拌机三部分组成,进料仓在电机的驱动下向秤斗送出物料,秤斗支撑在称重传感器上,由传感器及变送器产生的代表重量的电信号经信号放大模块后再由PLC与计算机采集,当达到预定重量时,PLC 驱动电机开启秤斗门,物料进入搅拌机,同时启动搅拌电机,搅拌到规定时间后开启出料口放料,一次配料过程完成。控制系统组成框图如图2所示,

称重传感器的信号0-30mV接进变送器信号器放大模块处理后,将其重量变化为0-30mV(可用于1-3 mV/V电阻应变传感器)的标准信号转换为DC电压输出:0-5V,1-5V,0-10V或电流输出:0-10mA,0-20mA,4-20mA,进行数据处理后以串行通信方式传给PLC的AD采集模块,PLC 将接收的数据送入触摸屏或上位机程序界面里显示,供操作员监控;当需进行混合配料时,由用户按自动键,PLC 启动加料阀门,将所需物料(本系统中含三种物料)按一定配比依次加入搅拌仓中,同时PLC监测料位计送来的脉冲信号判定物料所处仓中位置,从而控制加料阀门的通断;加料完成后,根据预置的混和延迟时间,PLC 启动搅拌电机,保证物料在搅拌仓中充分搅拌,完成混料操作;然后进入放料和压料阶段,由PLC 控制出料阀门动作,将物料从搅拌仓中输出,压入储料罐中,完成一个周期的自动配料控制工艺流程。
其中称重采用梅特勒--托利多称重传感器,信号变送器采用TR200H。F900是三菱公司推出的通过密封键盘提供操控和过程监视的操作员面板,它支持文本和图形显示。
五种骨料仓,每种仓都有慢、快配料门,卸料门 共三种门
五个骨料仓共五个骨料秤
骨料1配料秤:启动 停止 完成 归零 重量值与目标值无振
重量值显示:
目标值显示:
粗配 精配 卸料
骨料2配料秤:启动 停止 完成 归零 重量值与目标值有振
重量值显示: 振 共是两个振动器
目标值显示: 振
粗配 精配 卸料
骨料3配料秤:启动 停止 完成 归零 重量值与目标值无振
重量值显示:
目标值显示:
粗配 精配 卸料
骨料4配料秤:启动 停止 完成 归零 重量值与目标值有振
重量值显示: 振 共是两个振动器
目标值显示: 振
粗配 精配 卸料
骨料5配料秤:启动 停止 完成 归零 重量值与目标值有振
重量值显示: 振 共是两个振动器
目标值显示: 振
粗配 精配 卸料
外加粉2个仓叠加一起共用一个秤:
外加粉1加料门 外加粉2加料门 共用1个卸料门
外加粉配料秤:启动 停止 完成 归零 重量值与目标值有振
重量值显示: 振
目标值显示: 振
螺旋1 螺旋2 卸料
煤粉灰2个罐叠加一起共用一个秤:
煤粉灰1加料门 煤粉灰2加料门 共用1个卸料门
煤粉灰配料秤:启动 停止 完成 归零 重量值与目标值有拱振
重量值显示: 拱
目标值显示: 振
螺旋1 螺旋2 卸料
煤粉灰2个都有高位与低位检视
水泥4个罐叠加一起共用一个秤:1 2 3 4 加料门 共用1个卸料门
煤粉灰配料秤:启动 停止 完成 归零 重量值与目标值有拱振
重量值显示: 拱
目标值显示: 振
螺旋1 螺旋2 3 4 卸料
水泥4个罐都有高位与与低位检视
外加剂1仓:
外加剂配料称:启动 停止 完成 归零 重量值与目标值无拱无振
重量值显示:
目标值显示:
计量 卸料
外加剂2仓:
外加剂配料称:启动 停止 完成 归零 重量值与目标值无拱无振
重量值显示:
目标值显示:
计量 卸料
水箱:大管进水快水配料门 小管进水慢水配料门
配料秤: 启动 停止 完成 归零
重量值显示:
目标值显示:
粗配 精配 清洗 卸料
按钮-开关-控制:
面板骨料下方的平带输送:启动 停止 斜带:启动 停止
搅拌机:启动 停止
搅拌缸:开门 关门
电铃:自动响铃 手动响铃
水箱:大管进水 小管进水 卸水
传感器信号传感器接线盒,再由接线盒接入变送器,变送器技术资料:
工作电源:DC11-33V(AC15-24V) 耗电量:1-3W
工作温度:-5摄氏度至+50摄氏度 工作湿度:小于90%相对湿度
传感器型式:所有电阻应变测力传感器或0-30mV信号转换
传感器激励:提供直流10伏±2%,最大供电120毫安。
输入灵敏度:讯号输入0-30mV(可用于1-3 mV/V电阻应变传感器)
滤波:第一级10ms固定动态滤波(开/关选择)
第二级5-250ms可调滤波(9档可选)
精度:分辨率≥65000分度,线性度:≤0.003%,
温度系数:±25ppm/℃ 输出:(纹波≤5mvpp)
第一路DC电压输出:0-5V,1-5V,0-10V负载电阻≥2KΩ
第二路电流输出 :0-10mA,0-20mA,4-20mA负载电阻≤420Ω
零位可调范围:0-20mV,量程可调范围:2-30mV,以上为25转可调式电位器。
2.2 主要控制功能设计
(1)具有断电保护功能:如果在加料过程中出现断电情况,则应保护现场,一旦来电后先显示提示画面等待按键,如果是停止键,则清除断电保护状态,返回初始工作状态;如果是暂停键,则恢复断电时的工作状态继续工作;
图4 单独加料子程序流程图
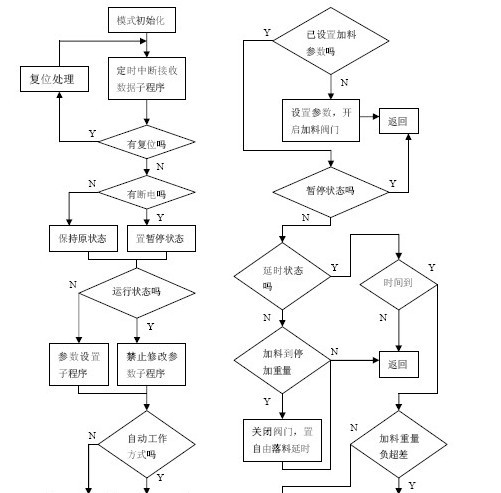
(2)设置“自动”和“手动”两种工作方式:“手动”工作是单独完成某个控制环节,如单独“加料”,单独“搅拌”和单独“放料”,它允许用“暂停/继续”键进行暂停,允许在暂停状态修改参数;“自动”工作是完成一个完整的循环控制周期,它包括加料、搅拌、放料等环节,“自动”操作时只允许“暂停/继续”键有效,各“手动”键无效,且不能修改参数;
(3)具有立即停止功能:当“停止”键有效时,任何控制过程中将停止并返回到重量显示状态;
(4)具有置零功能:在称重状态下按“置零”键,可使显示值回零,如果超过置零范围则不能置零并显示出错信息;
(5)具有去皮功能:在称重状态下按“去皮”键可将显示重量作为皮重扣除,再按一次“去皮”键将恢复原来的显示重量。
3.提高系统称重精度的措施
系统的精度主要由传感器和信号放大模块决定,但由于系统的工作过程是一个动态过程,控制过程中的某些操作将直接影响到系统的精度,因此在软件上采取了以下措施:
(1)在每一配料周期开始时,将此前设定的加料量与实际的加料量求差值,作为本周期设定的加料量的补偿值,以消除每一秤加料量的累计误差;
(2)不采用开机自动置零方式,目的是为了便于观察称重传感器的工作情况,在称重罐无附加重量的情况下开机后所显示的重量值如果超过标准重量的30%,则应考虑传感器是否出现故障需要更换;
(3)在系统实际工作过程中,由于机械振动设备磨损及秤体积尘等原因还会造成预加压力的改变而使零点电压变化,为了确保测量值的准确,系统软件定时对零点电压进行自动测量,然后在计算中扣除零点值。自动测量的方法如下:在单片机定时中断周期到时,单片机系统输出复位信号传给PLC,由PLC 关闭电机,停止加料,然后控制系统运转一定时间,将料放尽后进行测量,将测量出的零点电压值存入暂存区;
(4)加料过程中,当理论用料量和实际的加料量的差值小于加料提前量时,关闭加料阀门,停止加料,靠惯性和阀门关闭后的物料流量补足理论料量,若提前量太大,采用点动方式完成(即对送料电机采用脉冲驱动方式,每启动一次,只送入少量物料),以保证称重的准确性。通过采取以上措施后,系统的称重精度达到了3/1000。
备注:
本混凝土搅拌站生产自动化控制系统是不需要秤重仪表的,计量系统计量值在计量局检验的实际过程中,按照我们以往的经验,往往不是说去针对某个传感器,某个信号变送器,或者别的零配件进行检定,而是针对整个系统进行检定。
检定的方法也很简单,就是放置一个标准砝码,如500kg,看在我们系统的终端显示上面,如电脑或PLC或仪表上面,是否也是显示500kg这个数值(当然,允许有一定范围的误差的),如果是,那这个系统就是合格的。像现在比较常见的地磅、汽车衡等都是检测整个系统的,而不是说要把我们自动化系统中的传感器什么的单独拿出来检测的。
另外,即使非要检测传感器,传感器现在都有生产许可证,变送器不会检测的,我们自动化系统的设计师完全自信地告诉质监局,该产品只是一个信号放大的作用而已,就是将传感器出来的信号(一般为0——30mv)进行放大,放大出来的信号是0——10V或者4——20mA,这个信号如果也要检测,可以用万用表检测出来的。也可以按照TR200H的使用说明书中的标定方法,进行检测,这个都是标准的信号出来的,可以放心让质监局去测试。详细的标定方法可以看看说明书。
所以,关于质监局计量我们的计量系统的事宜,我们的计量系统这边在电脑或者PLC上面的信号处理是比较正常的,就能达到计量测试要求。
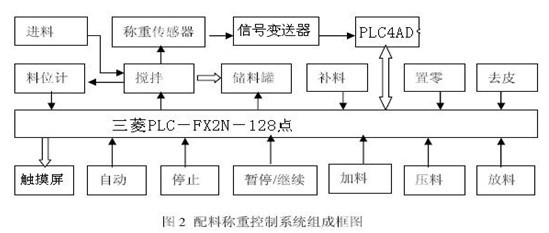
(2)设置“自动”和“手动”两种工作方式:“手动”工作是单独完成某个控制环节,如单独“加料”,单独“搅拌”和单独“放料”,它允许用“暂停/继续”键进行暂停,允许在暂停状态修改参数;“自动”工作是完成一个完整的循环控制周期,它包括加料、搅拌、放料等环节,“自动”操作时只允许“暂停/继续”键有效,各“手动”键无效,且不能修改参数;
(3)具有立即停止功能:当“停止”键有效时,任何控制过程中将停止并返回到重量显示状态;
(4)具有置零功能:在称重状态下按“置零”键,可使显示值回零,如果超过置零范围则不能置零并显示出错信息;
(5)具有去皮功能:在称重状态下按“去皮”键可将显示重量作为皮重扣除,再按一次“去皮”键将恢复原来的显示重量。
3.提高系统称重精度的措施
系统的精度主要由传感器和信号放大模块决定,但由于系统的工作过程是一个动态过程,控制过程中的某些操作将直接影响到系统的精度,因此在软件上采取了以下措施:
(1)在每一配料周期开始时,将此前设定的加料量与实际的加料量求差值,作为本周期设定的加料量的补偿值,以消除每一秤加料量的累计误差;
(2)不采用开机自动置零方式,目的是为了便于观察称重传感器的工作情况,在称重罐无附加重量的情况下开机后所显示的重量值如果超过标准重量的30%,则应考虑传感器是否出现故障需要更换;
(3)在系统实际工作过程中,由于机械振动设备磨损及秤体积尘等原因还会造成预加压力的改变而使零点电压变化,为了确保测量值的准确,系统软件定时对零点电压进行自动测量,然后在计算中扣除零点值。自动测量的方法如下:在单片机定时中断周期到时,单片机系统输出复位信号传给PLC,由PLC 关闭电机,停止加料,然后控制系统运转一定时间,将料放尽后进行测量,将测量出的零点电压值存入暂存区;
(4)加料过程中,当理论用料量和实际的加料量的差值小于加料提前量时,关闭加料阀门,停止加料,靠惯性和阀门关闭后的物料流量补足理论料量,若提前量太大,采用点动方式完成(即对送料电机采用脉冲驱动方式,每启动一次,只送入少量物料),以保证称重的准确性。通过采取以上措施后,系统的称重精度达到了3/1000。
备注:
本混凝土搅拌站生产自动化控制系统是不需要秤重仪表的,计量系统计量值在计量局检验的实际过程中,按照我们以往的经验,往往不是说去针对某个传感器,某个信号变送器,或者别的零配件进行检定,而是针对整个系统进行检定。
检定的方法也很简单,就是放置一个标准砝码,如500kg,看在我们系统的终端显示上面,如电脑或PLC或仪表上面,是否也是显示500kg这个数值(当然,允许有一定范围的误差的),如果是,那这个系统就是合格的。像现在比较常见的地磅、汽车衡等都是检测整个系统的,而不是说要把我们自动化系统中的传感器什么的单独拿出来检测的。
另外,即使非要检测传感器,传感器现在都有生产许可证,变送器不会检测的,我们自动化系统的设计师完全自信地告诉质监局,该产品只是一个信号放大的作用而已,就是将传感器出来的信号(一般为0——30mv)进行放大,放大出来的信号是0——10V或者4——20mA,这个信号如果也要检测,可以用万用表检测出来的。也可以按照TR200H的使用说明书中的标定方法,进行检测,这个都是标准的信号出来的,可以放心让质监局去测试。详细的标定方法可以看看说明书。
所以,关于质监局计量我们的计量系统的事宜,我们的计量系统这边在电脑或者PLC上面的信号处理是比较正常的,就能达到计量测试要求。